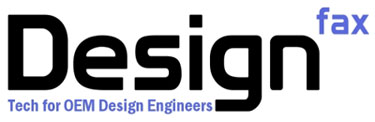
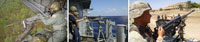
Honing .50-caliber machine gun barrels no easy shot
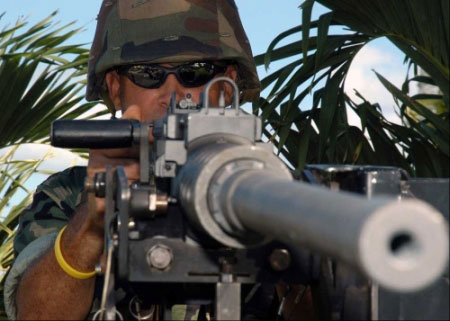
Few weapons on the battlefield are feared more than the M2HB .50-caliber machine gun. Designed almost 90 years ago by John M. Browning and affectionately called "Ma Deuce" by troops on the trigger end of the gun, the M2 and its variants are widely used by the U.S. military on land, sea, and in the air. It launches a 0.510-in. dia. slug, typically weighing 750 grains (1.71 oz), at 3,000+ fps, delivering 10,000 to 13,000 lbf of energy on a target. For comparison purposes, that's equal to 12 M16 bullets of .223 caliber. The M2 is revered for its effective range of up to 2,000 m and multi-purpose capability against lightly armored vehicles, personnel, hardened fortifications, aircraft, and light naval craft. The M2 is usually vehicle-mounted or in a fixed position, though infantry can hustle it around, too.
"Ask the man who owns one" is a 1950's advertising slogan that still rings true, and if America's war fighters are to be believed, the .50-caliber machine gun barrels made by U.K.-based Sabre Defence Industries are the best in the business. Part of the reason for that preference, officials at the company’s Nashville plant believe, is the superior accuracy and easy cleaning that result from the excellent bore geometry and surface finish imparted by a Sunnen HTB tube hone. Since installing the hone, test groups from sample barrels have tightened up nearly 100% over the Army's requirement.
U.K-based Sabre acquired the Nashville facility in late 2002. "We have been making military .50-caliber barrels and guns since 1979, as well as commercial rifle barrels for various companies over the years, and the new owner, Guy Savage, planned to reposition our operation to be about 50/50, military and commercial," says Charles Shearon, general manager of the Nashville plant. "Our operation was to be a launch pad for U.S. production of Guy's XR15/16 rifles — a premium variant of the AR15/M16 — for the civilian and police markets. The start of the Iraq war in early 2003 changed that. We received strong military orders for our .50-caliber machine-gun barrels, 7.62-mm M60 machine gun barrels, M134 minigun barrels, M6 weapons mount, and various components." The demand for .50-caliber barrels grew in the next few years from about 100 per month to 1,200 per month, and employment at the plant ramped up from 15 to 85.
Sabre makes two variations of the .50-caliber barrel: the heavy barrel for the M2 Browning gun and a lighter, shorter version for the M3 aircraft machine gun. Both have a Stellite liner for the chamber throat and first few inches of rifling. The liner and a retainer for attaching the barrel to the receiver are both shrink-fitted. The Stellite liner (75% cobalt and 25% chrome) withstands the intense heat and gas erosion of the initial discharge better than any ordnance steel.
The heavy barrel starts as a 45-in. piece of bar stock, 2.625-in. in diameter, weighing about 73 lb. "For the heavy barrel we use MIL-S-46047, a special alloy with extra vanadium to increase life," Shearon explains. "The aircraft barrel is MIL-S-11595, which we also use in our commercial guns and pass the quality advantage on to our customers. We have to buy these steels by mill run. The heavy-barrel material is cut by the mill and heat treated when we receive it. We do some preliminary operations to prep it, then gun-drill the chamber end with a 0.75-in. hole about 11 in. deep. A temporary liner is then installed, and the rest of the barrel is gun-drilled with a 0.490-in. hole. We ream after drilling, and have a hole-size tolerance of ±0.001 in. at that point, but the next step is to stress relieve, and that often changes the bore. Honing allows us to control the bore's final geometry and hole size to a fraction of the allowable MIL-Spec, which is helpful because of the small variations introduced later with button rifling and chrome plating."
Sabre had been using a manual lapping machine to finish bores, but the increase in military orders resulted in a bottleneck of work at that operation. "Sunnen's senior field engineer in our area, Ron Williams, has always been helpful to us, so we consulted him on how current technology could improve our processes and output," says Shearon.
|
The result was installation of a Sunnen HTB-2000 tube hone system in early 2006. Equipped with Borazon CBN stones, a traveling steady rest, and whip-guide bushings, the PLC-controlled machine has an output of 10 to 12 barrels an hour, compared to about one an hour with the old process. "The load-sensing system on the machine automatically adjusts the stone feed for optimum stock removal without tool crashes, which reduced our labor and helped improve output," explains Garry Hogan, Sabre's plant manager. "More important to us is the automatic gaging system. The machine gages the bore after every stroke, allowing us to control hole size, roundness, and straightness to 0.0005 in. without operator intervention. Even after button rifling and plating, we are able to stay well below the MIL-Spec of ±0.004 in. on bore dimensions, which is quite a feat on a bore length of 33 in. Tool life for the process varies with the amount of stock removal, which typically runs 0.002 to 0.004 in.”
|
|
Hogan says the crosshatch pattern that honing leaves on the bore surface aids in rifling the barrel by maintaining a consistent lubricant film. To create the rifling, a 0.517-in. carbide button is pushed through the bore, which is 0.503 in. at this stage. The button has the rifling form in high relief on it, and is rotated at the correct twist rate. The lands on the button engrave the grooves in the bore. "The very round hole we get with the hone helps prevent high and low spots in the rifling, and keeps the grooves concentric with the bore, all of which aid accuracy," Hogan adds. "We're unique in the business in that we make our own buttons, too, which gives better control of our quality."
|
Surface finish of the bore coming off the hone is approximately 20 µin. Ra and drops into the low teens after button rifling, significantly exceeding the MIL-SPEC of 63 µin. This helps to maximize muzzle velocity and makes it harder for metal and powder fouling to get a toehold, so cleaning is easier. "In the precision rifle shooting community, the sweet spot for surface finish is considered 10 to 20 µin.," explains Hogan. "Though it seems contradictory, a smoother surface actually increases surface contact and friction with the bullet jacket, causing increased copper fouling."
After contouring the exterior of the barrel, the bore is chrome-plated to a thickness of 0.0013 to 0.0020 in. "One of the reasons we run such tight tolerances off the hone is because we lose some tolerance in the plating process," Hogan explains. "The platers are excellent and seldom vary more than 0.0005" in., but if they do, we already have some margin for error to work with."
The Stellite liner starts as a casting, which Sabre gun drills and reams, then sends to a third party for honing. "This supplier has never scrapped a part, so it's a good system that we're not going to fix,” Hogan adds. With the barrel induction-heated and an alignment gage in place, the Stellite liner is pressed into the barrel's chamber so that its lands and grooves line up perfectly with those of the barrel.
|
Every barrel is then fired with a high-pressure test round and examined with a Sunnen magnetic particle inspection system. "We're required to test-fire a certain number of barrels from each lot for accuracy," Shearon says. "The Army's spec calls for a 10-round burst to hit within an 8-in. circle at 100 ft. We've always been able to hit 7 in., but since we started honing we're hitting 4 in."
According to Sunnen's Ron Williams, Sabre's experience is not unusual. "Honing is earning new respect from barrel makers, whether it's pistol, rifle, shotgun, or even paintball," he says. "One leading maker of special-purpose rifle barrels both rough-hones and finish-hones. They are perfectionists who hold ±0.000050-in. roundness and a tenth or better size the entire length of the barrel."
"We're lucky to be able to interact with users of our products," Shearon says. "At a recent armor war-fighting symposium at Ft. Knox earlier this year, we had several tank gunners tell us they knew as soon as they shot a .50 if it was a Sabre barrel or not. If it wasn’t, they found one of ours and installed it. We're sure our commercial rifles will earn the same loyalty, too, as we ramp up production and get the word out."
Want more information? Click below.
Sunnen Products Company
© Nelson Publishing, Inc. All Rights Reserved