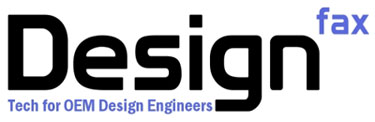
Wheels:
Twin turbos, direct injection give Ford's gasoline engine an EcoBoost
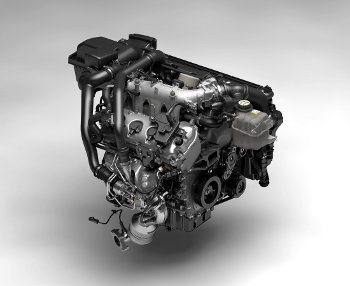
EcoBoost engine: The new 3.5-liter engine is the first in a wave of EcoBoost engines coming from Ford as part of a strategy to bring affordable fuel efficiency improvements to millions.
Ford’s new “downsize and boost” strategy is hinging on its 3.5-liter EcoBoost gasoline V-6. The twin-turbocharged, direct-injection engine aims to provide consumers with up to 20% better fuel economy, 15% fewer CO2 emissions, and better driving performance versus larger displacement engines.
EcoBoost will first be available this summer on the 2010 Lincoln MKS, Lincoln MKT, Ford Taurus SHO, and Ford Flex, expanding availability to 90% of Ford’s nameplates by 2013.
The EcoBoost system uses two Honeywell GT15 turbochargers — one on each bank working in tandem — to harness exhaust gas to pump V-8 power out of the smaller-displacement V-6 engine. The technology, in conjunction with direct fuel injection, allows EcoBoost to punch above its size in terms of power and responsiveness.
Close collaboration between Ford and Honeywell created a system that met Ford’s rigorous durability and safety criteria with such accuracy that the driver never notices the turbocharger operation. Sophisticated electronic controls balance boost and torque levels to give the driver the feeling of continuous torque delivery without turbo “whines” and “whooshes” that characterized some previous-generation turbocharger engines.
“One of the principles behind EcoBoost is that it isn’t intrusive,” says Keith Plagens, Ford turbo system engineer. “EcoBoost delivers added power seamlessly. Using Honeywell’s GT15 turbochargers gave us the performance feel and low-end response our customers demand.”
The turbocharger system features a pressure-controlled waste gate with an internal valve set at the Honeywell factory to within 3/10ths of a psi. “That means our side-to-side balance is well controlled and, again, gives the customer seamless operation,” Plagens says.
Exhaust gas flowing through the turbocharger spins a turbine wheel at very high speed (approximately 170,000 rpm) that drives a compressor turbine on the clean-air side of the turbo. This fan effect densely packs intake air into the engine — compressed air up to 12 psi that results in increased performance. With its twin turbochargers, the EcoBoost V-6 swallows about 25% more air than its normally aspirated cousin, the 3.5-liter Duratec V-6.
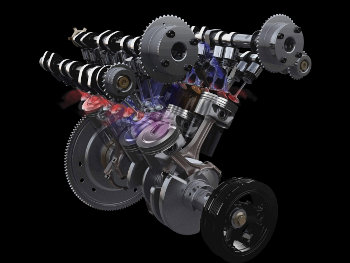
EcoBoost engine in action: Spent gasses are pushed through the exhaust valves, where they are routed to the turbochargers for the efficient conversion of exhaust gasses into energy to drive the turbochargers.
The EcoBoost approach eliminates several customer worries from previous turbocharger applications. Designed for long-life reliability, EcoBoost’s turbochargers feature water-cooled bearing jackets. This architecture is designed to prevent oil “coking” that could occur in previous-generation turbochargers. The new design means that EcoBoost drivers don’t need to observe special operating precautions, such as idling the engine before switching it off. The turbochargers are designed for a life cycle of at least 150,000 miles or 10 years.
Fuel-charging system
Most fuel systems also are broken into subsystems such as fuel pump, fuel lines, fuel rails, and injectors. But there are significant common factors that affect the entire system performance, such as fuel flow, thermal distribution, fuel distribution, NVH, and hydraulic pulsations. Those input factors require system tuning and design techniques to improve the whole system performance, which is achieved by combining the technical expertise and resources offered by the supplier and OEM.
“Our own Ford Vehicle Benchmarking Center showed that many suppliers applied a common practice design approach of ‘one size fits all’ and with little consideration as to how the subsystems could be fine-tuned for optimized function and performance,” says Joseph Basmaji, Ford direct-injection fuel system technical specialist.
For example, hydraulic pulsations (or hammering) is a common issue in all direct-injection fuel systems and can cause a range of issues, from poor fuel distribution to component durability. Knowing how to address these pulsations in each of the subsystems is critical to being able to effectively reduce the pulsations of the entire system to an acceptable level and achieve optimized performance.
Teams from Ford and Bosch worked for months to develop hydraulic models and prototypes to provide the data leading to optimized orifice sizing, placement, and spacing in order to tune in the hydraulic frequencies in each of the subsystems. “As a result, hydraulic pulsations to the entire system could be reduced, providing better fuel distribution for improved component durability, function, performance, and reduced emissions,” Basmaji says.
Another new approach used on the EcoBoost engine is the bolting pattern for the high-pressure fuel rails. Ford’s collaboration with Bosch led to a fastening design concept that incorporates a criss-cross pattern across the rail, as opposed to brackets on one side of the rail only. This pattern reduces the moment arm on the rail as well as some of the high stresses that can result because of the tendency for the rail to lift under the 2,150-psi hydraulic pressure of the fuel.
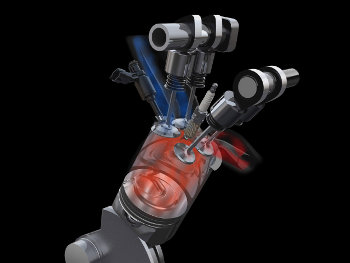
EcoBoost engine in action: The fuel injectors are mounted at the side of the combustion chamber. The spark plug is at the top of the chamber.
Ford and Bosch also developed a new Y-pipe fuel delivery system, rather than a conventional multi-pipe system, to feed the fuel rails. The Y-pipe method provided several advantages in a direct-injection system, including reduced pulsations, hydraulic frequency separation, improved fuel distribution, and assembly improvements. The Y-pipe also fills both rail halves simultaneously, as opposed to a multi-pipe system, where one rail must fill completely before filling the other rail. This solution reduces green start times at the vehicle plant as well as vehicle start time in the field.
“Development of the Y-pipe was a first for us and a first for Bosch,” Basmaji says. The Y-pipe also provides better fuel thermal distribution, minimizing fuel distribution issues from fluid density changes. “The result is a more-precise delivery of the fuel mass required for a more-efficient fuel burn in the combustion chamber and better fuel economy,” Basmaji says. “The fuel distribution is improved bank to bank as well as injector to injector. That’s very critical and one of the major reasons our fuel-charging system runs as well as it does.”
Engine boot camp
To ensure the EcoBoost V-6 engine delivers quality performance, a team of engineers subjected it to an extensive battery of tests as part of the company’s engine “boot camp.”
“EcoBoost was engineered with a relentless, disciplined focus on quality that required a zero-defect mindset from engineers and our supplier partners,” says Derrick Kuzak, Ford group vice president of Global Product Development. “The finished product will represent the best combination of production-ready engine technologies of today, poised and ready to deliver the performance, fuel efficiency, and value that customers expect.”
The extensive testing to prove out the 3.5-liter EcoBoost V-6 engine was accomplished through three avenues: using computer aided engineering models (CAE), in the lab with dynamometers, and on roads in the real world. Between testing on the dyno and in the field, EcoBoost engines have racked up the equivalent of more than 1 million miles of customer driving.
The rigid testing included 20 individual dynamometer-level tests designed to push the engine to its limits. The testing protocol verified the reliability of the complete engine system under maximum engine speeds and loads, coolant and oil temperature, and customer driving patterns.
The Road Cycle Durability test, for example, is designed to replicate real-world customer driving and vehicle maintenance patterns. For this test, engines with EcoBoost technology were subjected to 1,000 cold starts, followed by sustained operation at peak torque and peak power. During the course of the test, engine coolant temperatures ranged from 12°C (about 53°F) to 95°C (203°F).
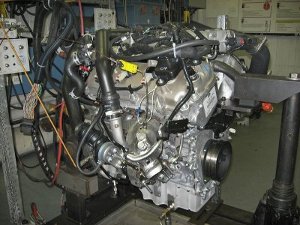
EcoBoost put to the test: The 3.5-liter EcoBoost V-6 accumulates thousands of hours on the Ford dynamometer to verify the reliability of the complete engine system. During the punishing testing, engine performance is examined under maximum engine speeds and loads, coolant and oil temperatures, and customer driving patterns.
In total, this single test required 1,000 hours of extreme engine operation, representing more than 60,000 miles of customer driving.
“This was a critical test for us, and the EcoBoost fleet passed with flying colors,” says Brett Hinds, Ford’s advanced engine design and development manager. “We’re confident that EcoBoost is ready to provide consistent performance in varied conditions.”
Individual components underwent rigorous proving, as well. EcoBoost’s twin turbochargers, for example, are designed to run at a very high temperature — up to 950°C (1,740°F). Ford engineers proved out the turbochargers by running them at 950°C for 10 minutes and then “shocking” the turbos by running them at room temperature for 10 minutes. The tests were repeated at maximum boost continuously for hundreds of hours, under far more severe conditions than customers are expected to dish out.
EcoBoost also endured Ford’s standard engine durability test signoff running at maximum revs and turbo boost for the equivalent of 15 straight days or 360 hours.
To produce the new line, Ford has invested $55 million to retool and reopen Cleveland Engine Plant No. 1, which had been idled in 2007.
To ensure quality is built into the engine from the outset, Ford has developed a new, internal database for its operations. Each engine will be built with a sophisticated, embedded engine “birth history” that allows plant engineers to track every stage of production.
The engine history, maintained in a microchip database, includes hundreds of metrics and allows engineers to trace the precise path taken by any part so any quality control issue can be traced back to its source.
Source: Ford Motor Company
© Nelson Publishing, Inc. All Rights Reserved