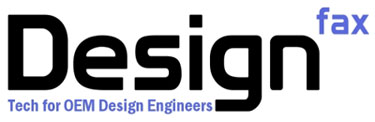
Motion Control News
World land speed record challengers push for 1,000 mph
There's a healthy rivalry brewing between the U.S. and U.K. over the world land speed racing record. The Brits took it from the U.S. in 1997, and now the U.S. wants it back.
In 1904, none other than Henry Ford himself drove 91.37 mph to capture the World Land Speed Record title. Today the record stands at just over 763 mph, captured by the British on October 15, 1997 with the ThrustSSC jet-powered car.
Now, an American/Canadian team in Washington State has a 50,000-hp converted F-104 jet car ready to travel over 800 mph to bring the record back to the U.S. The vehicle is 56 ft long and weighs 13,000 lb.
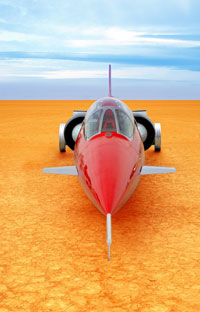
The North American Eagle [Image: Douglas Schwartz Photography]
"I'm in discussions with the Edwards Air Force base to conduct midrange test runs early next year on Rogers Dry Lake (where the Budweiser Rocket Car drove 739 mph 1979)," says Ed Shadle, owner/driver of the North American Eagle. "Once the midrange testing (up to 600 mph) is complete, we'll be poised to go for the record whenever the weather conditions are optimal at Black Rock, NV, or another undisclosed location." Shadle is also evaluating a location near the area Steve Fossett was scouting before his untimely death. The aim is to set a new mark in 2009.
But not so fast, American Eagle. The Brits have plans that are one big step — or 200 mph — ahead.
U.K. engineers aim to create a 1,000-mph jet car — and inspire a new generation of engineers along the way — with their Bloodhound Project. Three years (record target is 2011) is how long the team lead by Richard Noble, the current world land speed record holder, figures it will take to create a car capable of traveling faster than a speeding bullet. Noble plans to get all of England involved in the project. He figures that the more minds involved in the project (from grade school to post-doctorate), the more of a chance that Bloodhound has to achieve its engineering and educational impact.
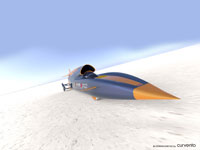
Conceptual drawing of the Bloodhound. [Image courtesy: curventa]
The Bloodhound Design team, lead by John Piper (JCB Dieselmax chief designer), has been working with University of the West of England (UWE Bristol) engineers and technicians in secret since January 2008, using the specialized facilities at UWE to help realize the formative stages of the project.
“We have held the World Land Speed Record for the last 25 years and we still hold it," says Noble. "There is early competition developing, and we have to defend our record. But our number one objective in this project is to create a national surge in interest in engineering and STEM [Science, Technology, Engineering, and Mathematics] subjects. We have discovered during the Bloodhound SSC research program that the education objective generates huge interest."
Bloodhound will be 42 ft in length and weigh in at 12,800 lb. The wheels will need to survive a 10,500-rpm proof test, and the car will be powered by a Eurojet EJ200 delivering 20,000-lb thrust and a Falcon hybrid rocket delivering 27,000-lb thrust in a hybrid two-stage acceleration scheme. The design speed is 1,050 mph. That's some serious dreaming for a team that currently has only a wooden and plastic model, built using rapid prototyping and CNC routers, on display at London's Science Museum.
“The beauty of Bloodhound is the openness of the project," Noble says. "So many engineering projects in the real world are subject to extreme confidentiality for obvious commercial reasons, but Bloodhound’s development will be seen by millions as it evolves with live coverage on the Web. This very openness of Bloodhound’s development presents unprecedented opportunities for us to prepare students for the real world.”
"We can share the Bloodhound SSC technology openly because there are minimal design restrictions for the Land Speed Record vehicles, and therefore competitive cars tend to be completely different," continues Noble. "Thus an advantage for one competitor is not necessarily of value to another."
Follow the efforts of both teams (including their equally fascinating and perilous struggles for funding) using the following links:
Want more information? Click below.
North American Eagle
Want more information? Click below.
The Bloodhound Project
Source: Compiled from Bloodhound Project and North American Eagle reports
Motion Control Products
Motion controller for high-end needs
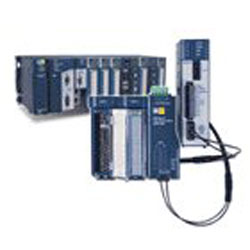
PACMotion is new motion controller designed to serve the high-end needs of complex motion apps. It is part of an integrated motion and machine logic solution, designed to provide performance, flexibility, and scalability for advanced machine automation. PACMotion module controls up to four axes plus a master axis; up to 10 modules can be placed in the PACSystems RX3i rack for control of up to 40 axes.
Using PACcore architecture, PACMotion is created to enable consistent performance and tight axis synchronization of all axes in the rack. As an integrated motion solution, PACMotion is designed to simplify programming by sharing a common database, eliminating complex data exchange between different programs, and reducing the learning curve required with two different programming languages, therefore boosting productivity. Paired with the FANUC servos, the motion controller provides a solution for machine automation.
Want more information? Click below.
GE Fanuc
Von Weise drop-in replacement AC gearmotors
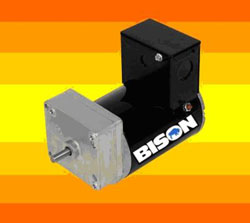
The VWDIR14 AC parallel shaft gearmotors are designed as Von Weise drop-in replacements and are also created to be compatible with most globally available AC power sources. Utilizing 1/20-hp (37.3 W) AC motors that can be operated from 115- or 230-V, 60- or 50-Hz power sources, the gearmotors are available in six standard, off-the-shelf models.
The VWDIR14 has gear ratios from 10:1 to 494:1 and continuous torque ratings up to 50 in.-lb. The enclosed, non-ventilated, permanent split capacitor (PSC) motors and integral gear reducers are reversible and feature all-position face mounting with a 50-lb overhung load capability. The gearmotors are available with UL and CSA recognition; CE recognition can be provided for OEMs.
Want more information? Click below.
Bison Gear & Engineering
Dual piezo motor drive ASIC
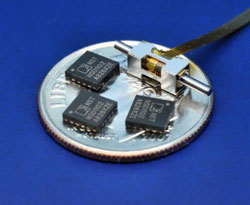
The NSD-1102 is a dedicated piezoelectric motor drive ASIC, designed for the Squiggle micro motors. The NSD-1102 can drive one or two SQL-1.8 Squiggle motors from a single 2.8- to 5.5-VDC supply. Users can control two micro motors independently using the ASIC’s standard I²C interface. The motor driver is housed in a compact 4 x 4 mm 16-pin QFN package. The NSD-1102 is created to take advantage of the Squiggle motor capabilities, which include 6-mm travel range, 0.5-µm resolution, speeds greater than 7 mm/sec, and stall force of 30 grams force.
The NSD-1102 includes an on-chip DC-DC step-up converter and four half-bridge drivers. A power-down mode provides minimal ASIC power consumption in stand-by, or the power can be turned off entirely and the motor will hold its last position. The motor and drive circuit draw 100 to 900 mW when moving, depending on motor speed and load. The NSD-1102 is also available on the MC-31DB driver, a printed circuit board that includes input/output connectors and all passive components. The ASIC and passives occupy a 6 x 9 mm footprint on the board. The MC-31DB can be used for system evaluation, as a reference design, or for integration into OEM systems.
Want more information? Click below.
New Scale Technologies
Medium-voltage soft-start motor controls
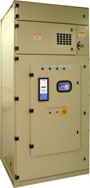
The HRVS-DN is a line of medium-voltage, soft-start motor controls, with ratings from 2.3 to 15 kV. The product is suited for a range of markets, including gas and oil, water-waste/water, mining, concrete and aggregate, as well as marine and industrial markets. The HRVS-DN is used to ensure smooth, step-less acceleration and deceleration of critical motors, eliminating high in-rush currents and mechanical shocks to the motor and the load. The product is manufactured under ISO9001:2000 and according to IEC, CE, DIN EN, and UL347 standards.
Want more information? Click below.
Solcon USA
Gear-driven goniometric cradles
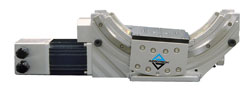
AGC motorized mechanical goniometers are used in applications where 90° of angular travel is needed with the payload at the center of rotation, or where two axes of rotation are needed about a common point. AGC goniometers can be mounted to standard optical tables, as well as standard Aerotech rotary stages. Performance includes ±12 arc sec accuracy, ±10 arc sec repeatability, 3.5 arc sec resolution, a maximum speed of 78°/sec, and a maximum load of 50 kg. This flexible stage series is suited for optical alignment, payload tip/tilt, beam steering, sensor calibration, laser applications, and other applications.
AGC goniometers can be mounted on one another to form a rotary system with all axes of rotation sharing a common intersection point. This allows compact pitch/roll/yaw systems to be created easily from a standard stage platform and without special adapter plates or mating fixtures. The drive mechanism is a precision gear and matched worm that are preloaded to reduce backlash. The stages include optical limit switches and hard stops to define a ±45° range of travel. The stage tabletops feature hard-coated aluminum, with stainless steel Heli-Coil inserts to prevent thread wear. Options include flexible motor selections, as well as a direct encoder mounted along the stage travel. Vacuum-compatible versions are also available.
Want more information? Click below.
Aerotech
Linear indexing drive with zero backlash
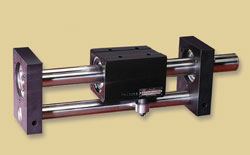
Available in seven sizes to meet axial thrust requirements from 22 to 450 lb, the Amacoil/Uhing RS indexing drive is designed to be a backlash-free alternative for linear motion systems. The inner race of the rolling ring bearings is in constant point-contact with the shaft. There is no play or free movement between shaft and bearings.
The RS linear positioning drive runs on a smooth shaft, with no threads where debris can get trapped. This provides built-in overload protection. If the system is overloaded, instead of jamming, the nut slips, which protects the components from damage. The RS drive also requires less downtime for cleaning threads or making repairs, resulting in more consistent production throughput rates. The series is available in five different linear pitch settings. The drives are suited for a variety of automated manufacturing processes in many industries, such as packaging, converting, textile, automotive, metrology, and CNC machining.
Want more information? Click below.
Amacoil
Ready-to-use servo drive controller
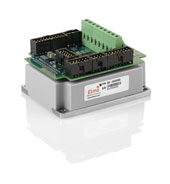
A new addition to SimplIQ core motion technology, the Solo Guitar is a versatile connection interface that is designed to reduce time when designing a PCB board. The controller can be easily set up and tuned using the company’s software tools.
The Solo Guitar operates from a DC power source in current, velocity, position, and advanced position modes. The device works in conjunction with a permanent-magnet synchronous brushless motor, DC brush motor, linear motor, or voice coil. The Guitar delivers up to 4.8 kW of continuous power or 5.4 kW of peak power in a compact package (46.7 x 61 x 80 mm or 1.84 x 2.4 x 3.15 in.). Other features include the ability to deliver 45 A of continuous current and 70 A of peak current, operate as a stand-alone device or as part of a multi-axis system, and support a wide variety of feedbacks. The Solo Guitar servo drive can be mounted anywhere, such as in a motor, in a machine, on a load, or attached to a moving part.
Want more information? Click below.
Elmo Motion Control
Extended range of stepper motor designs
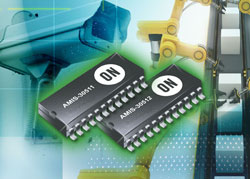
The AMIS-30511 and AMIS-30512 are two new serial peripheral interface (SPI) motor drivers that are capable of peak currents up to 800 mA. These new additions to the bipolar stepper motor control family are designed to eliminate the need for many external components.
The drivers contain two embedded H-bridges that can drive two-phase stepper motors with sustained peak currents up to 400 mA and maximum currents up to 800 mA for short duration. Each model also allows a host microcontroller to detect blocked rotor and end-of-run conditions without additional switches, Hall sensors, or optical encoders. In addition to stall detection, these functions allow the designer to program the microcontroller to calculate rotor position and to dynamically adjust current or speed. The 30512 contains a 5-V regulator to supply both internal logic and up to 50 mA for external components. Typical uses include security cameras, building and industrial automation, motor control, textile processing, process equipment, and robotics.
Want more information? Click below.
ON Semiconductor
Flat brushless DC miniature motor
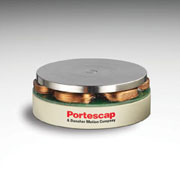
The nuvoDisc flat brushless DC miniature motor is designed to deliver maximum speed while minimizing size and vibration in medical and automation applications. With a diameter of 32 mm and a length of 11.8 mm, the nuvoDisc family of motors is over 75% shorter and 90% lighter than conventional flat motors, allowing engineers a greater ability to miniaturize apps without compromising performance.
Offering speeds up to 50,000 rpm and mechanical power output up to 30 W, nuvoDisc is created to deliver high efficiency. Compare it to other miniature DC motors. The motors are also designed to reduce power supply requirements by drawing less current.
Want more information? Click below.
Portescap
Brushless motor with integrated controller
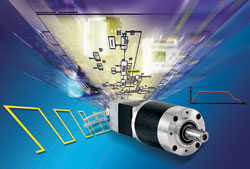
The Motomate brushless motor features a compact size, high efficiency, convenience, and easy programmability. Designed with an integral controller, the new motor provides an all-in-one solution for a range of applications where programmable movement of simple mechanisms is required. Typical uses include control of automatic doors and door lifts, access barriers, intelligent conveyor systems, among others.
Motomate incorporates a Crouzet built-in Milleneum2 controller, brushless motor drive, motor, and gearbox in a compact 2-1/2 x 6 in. package. With the power electronics incorporated directly inside the motor, the need for an external speed controller is eliminated. Motomate is available with a motor range of 30 or 80 W in several configurations. The motor produces up to 0.3 Nm in the direct-drive configuration, up to 3.5 Nm in the right-angle configuration, and up to 30 Nm in the planetary configuration. Other features include analog output and internal torque sensing capabilities for increased application flexibility. Intuitive programming with graphical function blocks allows easy programming of acceleration and deceleration in forward or backward motion. Reprogramming is done by using a PC or a removable memory module.
Want more information? Click below.
Crouzet North America
New ultra-compact precision positioning rotary stage
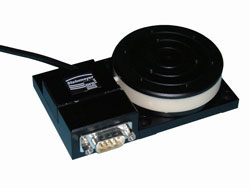
The DT 65-LM rotary stage offers a low-profile design with an overall height of 25 mm and length of 105 mm. This rotary stage weighs 0.35 kg, but can support loads up to 80 N. Driven by a piezo linear motor, the DT 65-LM has a positional accuracy of 0.015°, repeatability of less than 0.003°, and a maximum surface runout of 20 µm. Speeds up to 360°/sec and accelerations greater than 10,000°/sec² can be achieved.
The DT 65-LM is manufactured from a low-distortion aluminum alloy and is black-anodized. The stage is available with a direct-reading incremental angular encoder with 3,600 lines yielding a resolution up to 409,600 counts per 360°. Options include a 10-mm diameter center aperture, cleanroom and vacuum compatibility, and different encoder resolutions. The DT 65-LM is suited for applications in the semiconductor, fiber optic, medical/life sciences, optical, laser systems, and miniature robotics industries.
Want more information? Click below.
Steinmeyer
Motor protection system
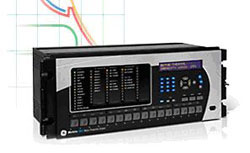
Designed for medium and large-size medium-voltage motors, the Multilin M60 motor protection system has new enhancements. The M60 now features remote resistance thermal detector (RTD) support, embedded IEC 61850 communications, enhanced security features, and ambient temperature monitoring and alarming.
With the remote RTD module mounted close to the motor and the ability to monitor up to 12 RTDs, the M60 is designed to deliver a cost-effective solution. The system offers communication capabilities, including support for the new Multilin HardFiber process bus solution. M60 also has programmable logic to build custom control applications, offering seamless communications and interoperability. The motor protection system includes added features for the highest levels of device and system security. It is designed to provide robust network security, while enabling critical infrastructure protection with dual permission access control and user command logging.
Want more information? Click below.
GE Digital Energy
Heavy-duty slide system
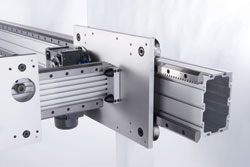
The HepcoMotion HDS2 heavy-duty slide system features larger-capacity bearings, assembled carriages, and two new sizes of construction beam. The system offers capacities up to 68 kN and provides flexibility for many sizes and types of heavy-duty components to be interchanged. The larger bearing sizes provide increased load capacity, including a 150-mm dia vee bearing and a 144-mm dia taper roller bearing. Slides and tracks are available in single-piece construction up to 4 m long and are supplied in single- or double-edge format in V slides or flat tracks.
The construction beams have multiple slide and track mounting options. The HDS2 also features a larger aluminum beam, which eliminates the need for machined steel. A compact version of the beam is ideal for small spaces, or it can be used to create a high-capacity Z-axis. When the extra rigidity of a steel beam is required, all slides can be fitted and aligned using the keyway option with dowel pins. HDS2 is available in component form or as a ready-mounted assembly with rack-driven carriages. Depending on the application, customers can select either high-precision ground slides or low-cost commercial slides.
Want more information? Click below.
Bishop-Wisecarver
Economical, stand-alone motion controller product
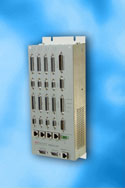
SPiiPlus SARLT is an RoHS-compliant controller that is designed to enhance the performance of OEM machinery requiring multi-axis synchronization. This 2-, 4-, 6-, or 8-axis controller features SPiiPlus PLC and CANOpen master support. The SPiiPlus SAR-LT can be implemented in systems with both servo and step motors and can support a range of modes. The controller has third-order profile generation with on-the-fly velocity, acceleration, jerk, and target position changes.
The SPiiPlus SAR-LT has a simple and convenient D-Type connectivity for interfacing with servo amplifiers, digital encoders, as well as analog I/O. The controller also features advanced logic capabilities and IEC 61131-3 programming, as well as expansion capability through its optional CANOpen interface. The SPiiPlus SAR-LT is based on the same control architecture as all SPiiPlus products, using a common programming language. The product is designed to operate standalone or with a host/MMI via Ethernet or serial communication.
Want more information? Click below.
ACS
Brush-commutated DC servo motors

MCG ID series is designed to offer improved motor-to-load inertia matching capability. These brush-commutated DC servo motors feature low cogging torque and simple brush commutation technology, which contribute to smooth operation at all speeds.
Offered in two frame sizes (NEMA 23 and 34), the motor can power equipment for a range of industry applications, including factory automation and robotics, machine tools, material handling, medical, among others. Depending on the model, standard motors in the ID23000 and ID33000 series can generate continuous torque from 0.212 Nm (1.88 lb/in.) to 1.59 Nm (14 lb/in.). Power ranges from 0.12 to 0.60 hp can be achieved, with speeds up to 6,000 rpm. Rugged IP42 construction contributes to motor reliability and longer service life. Motors can be customized with gearboxes, optical encoders, and other options to satisfy application needs.
Want more information? Click below.
AMETEK Technical & Industrial Products
Size 11 double-stack hybrid linear actuators
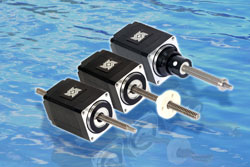
The 28000 series (Size 11) double-stack hybrid linear actuators are available in a variety of resolutions ranging from 0.000125 in. (0.003175 mm) per step to 0.002 in. (0.0508 mm) per step. The actuators deliver thrust to 30 lb (133 N). Models can also be micro-stepped for even finer resolution.
These compact linear actuators occupy a minimal 1.1-in.2 (28-mm2) space. The manufacturing processes incorporate engineering thermoplastics in the rotor drive nut and a stainless steel acme lead screw, engineered to assure reliability and performance. Applications include medical equipment, semiconductor handling, valve control, X-Y tables, hand-held instruments, telecommunications, and many more. In addition to standard configurations, the actuators can be customized to meet specific requirements.
Want more information? Click below.
Haydon Switch Instrument
© Nelson Publishing, Inc. All Rights Reserved